Total mixed ration (TMR) mixers have become a fixture on feedlots, dairies and mixed farms. They are the “must have” machines to process, mix and deliver multiple variations of feed to the livestock industry.
These heavy-duty blenders have improved feeding efficiency and provide exacting energy requirements without sacrificing the physical characteristics needed for proper rumen function.
Diversity
Allen Bonthuis of AIS Construction Equipment in Michigan and owner/operator of Farming Lean consulting group, says today’s mixers are much more diverse than before.
Read Also
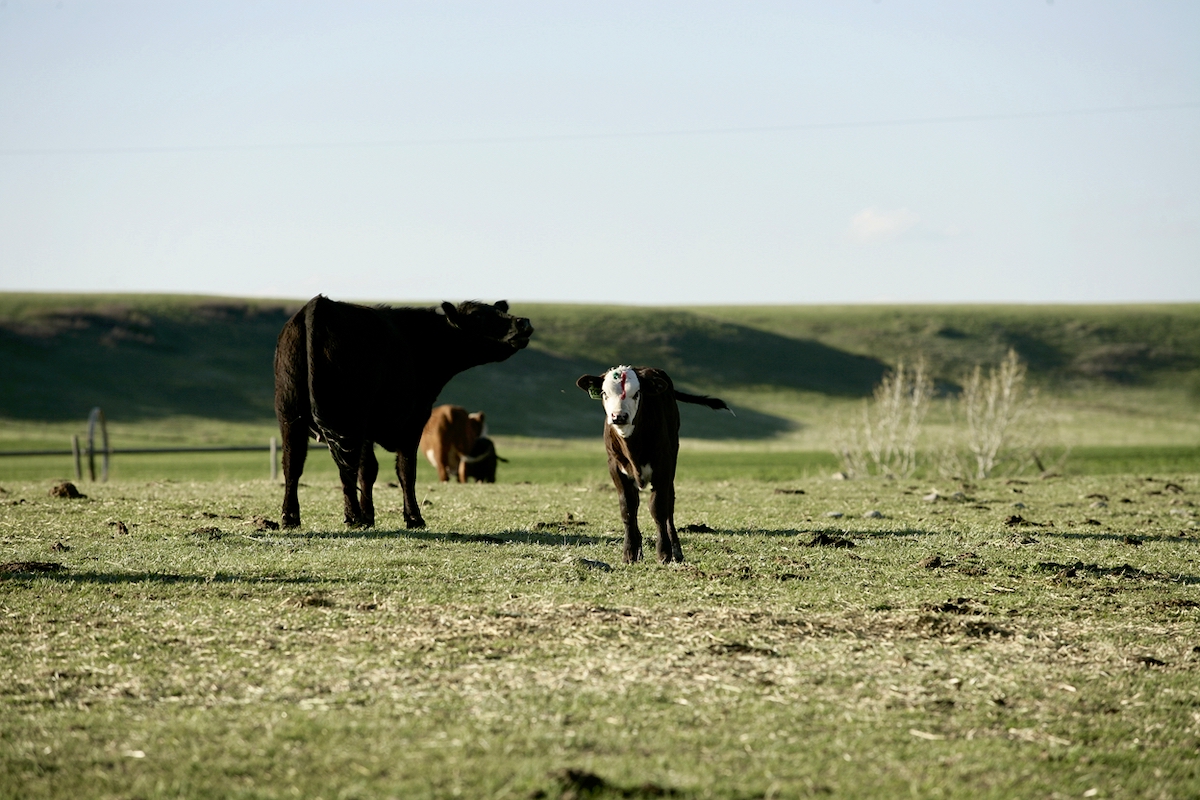
Body condition, nutrition and vaccination for brood cows
One of the remarkable events of the past century related to ranching has been the genetic evolution of brood cows….
“Everything goes in. Corn, silage, haylage or green grasses. More wet mixes, even trace or small minerals. Getting greenfeeds into a TMR used to be difficult but not now. Straw and dry hay along with wet products like corn gluten come out in a really consistent mix.”
Varied substances, often with different breakdown rates, enable improved nutrient use and allow for mixing more fringe products. Ration cost savings benefit the farmer, yet quantities of ingredients can be closely controlled.
Bonthuis believes accurately matching the machine size to the operation is just as important as the features it boasts.
“There is a huge range in size, almost as much as you can imagine. From a single-screw tank on small dairies to monster-sized four-screw mixers in large feedlots.” As an example, he says dairies often run anywhere from two to eight distinct rations, drastically affecting how the mixer is used.
“Each operation should consider their flexibility options. Could the mixer be doubled in size to cut the number of loads in half? Often the dollar difference between two pieces of equipment isn’t large enough to try to save that elusive buck.”
Technological advancements
Trevor Brady, general manager of Vanee Farm Centre dealerships in Lethbridge, Claresholm and High River, Alta., points to TMR technology upgrades during his years in the industry. Advances in hydraulics now allow some mixers to operate at slower speeds when starting, and a higher torque as they increase speed and reach capacity. The hydraulic feed discharge is also affected.
“As the load is coming down, it speeds up and it’s all pressure regulated hydraulically. It’s a very smart in-depth machine with load sensing to unload at a faster rate as we go down the bunk.”
GPS tracking is another significant change in many of the latest mixers. Brady says most feedlots are now using a feed management system. Signals from the office tell the operator what types of loads should go to which pens of cattle.
“GPS knows where the mixer is in the yard. If there is medication or a different mineral or supplement in a load and the truck pulls up to the wrong bunk, it won’t let it discharge.”
The management system also works with the mixer technology, simplifying the calculation and calibration process. It relays information such as pounds of grain, supplement, silage and mineral required in each load.
“It’s come so far. Not just in the TMR mixer but as part of the overall production technology. GPS and the management systems have changed much of how these feedlots are doing things.”
Types of mixers
The three main types of mixers have remained constant over the years with trailer, truck mount or stationary options.
Reel mixers provide a quick and gentle mixing of pre-processed feeds. Reels pick up material and gravity stimulates a tumbling action. Centre mixing bars help distribute the feed throughout the tank.
Horizontal mixers make up the bulk of feedlot machines. They work by compressing the ingredients rather than fluffing them like the reel mixers. Bottom augers move the product forward while upper ones grab it and send it rearward.
“Horizontals in this area are mainly going into the finishing lots,” says Brady. “They don’t handle straw or hay roughage that well. It can get tangled up in there, so they’re mainly for higher grain and silage rations. Most of them are truck-mounted.”
Vertical mixers have become the more popular equipment choice for operations using more forage and straw in their rations. Augers create a “boiling” action by lifting material upward, creating an up-and-down cycle. Ingredients move from the front to the back while baffles direct them around the tank.
“You could throw a round bale in and it cuts, chops, processes and discharges. They work for the cow-calf guy, dairies, even sheep and goats,” says Brady. “Farmers can use materials they weren’t able to before with horizontal or reel mixers.”
Options and features
Bonthuis says the newer-model vertical mixers come with engineered serrated or wavy-edge knives to provide excellent cutting actions.
Options include varying discharge door locations, stainless steel liners, unloading conveyors, heat-treated augers, Hardox steel flooring, tungsten-treated reversible self-sharpening knives on the augers and oversized tires for superior support in soft, muddy conditions.
Brady explains that at the end of the day, the mixed product still needs to get to the animals, and he believes reliability is the main focus for manufacturers.
“A cow-calf guy can put out a couple round bales if his TMR isn’t working, but not a dairy or feedlot. They can’t have that fluctuation in production. Reliability and up-time are everything to those operators.”
He believes with recent drought conditions over the last three to four years, there is even more value in the mixers.
“The price of feed has been so high in Western Canada, but TMRs blend a quality product and a mediocre product to keep the costs down. It’s helping operations stay alive. I think every livestock producer should have one. They’ve been revolutionary for the feeding industry.”
Bruce Derksen lives, works and writes in Lacombe, Alta. He has 30 years of experience as a hands-on participant in numerous branches of the western Canadian livestock industry.