The North American meat and poultry industry faced unprecedented challenges when the COVID-19 pandemic began to wreak havoc throughout the continent last spring. The many ways the industry tackled these challenges and returned to a semblance of normalcy in such a short time is one of the greatest stories in the long history of the industry.
Beef, pork and poultry processors on both sides of the border faced scenarios never before seen. Thousands of workers either became ill with the virus, were in contact with those who did or stayed home out of fear of contracting it inside plants. Absenteeism ran high and in one week in May U.S. beef plants ran at only 68 per cent of capacity. Huge cutbacks resulted in a dramatic decline in cattle and hog prices. U.S. cattle prices today remain six to seven per cent below year-ago levels.
Read Also
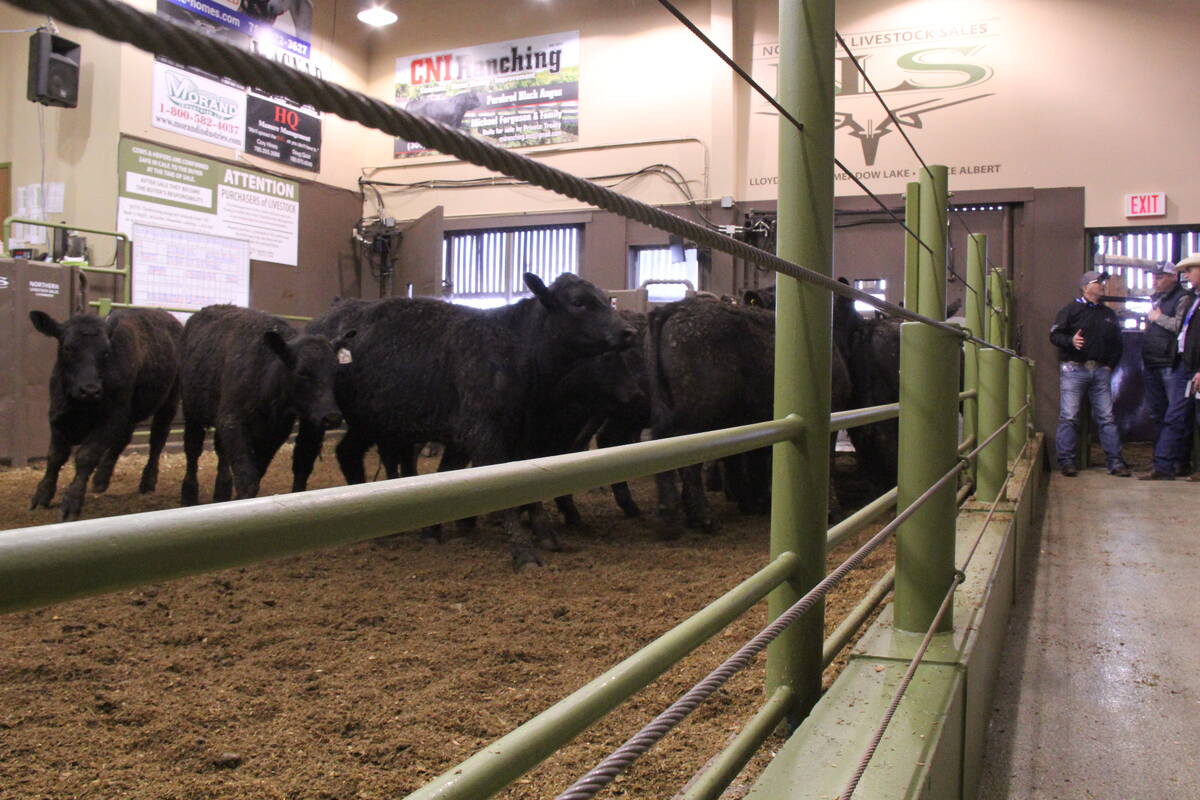
Canadian beef industry preparing for new traceability regulations
New livestock traceability regulations are expected to be ‘soft-launched’ in early to mid-2026
That production rebounded so quickly after May is because meat and poultry companies had already started spending millions of dollars to protect their workers. They have now spent well in excess of US$1.5 billion on numerous measures inside and outside plants. Meanwhile, they had to revamp production lines because widespread restaurant closures and restrictions transferred consumers’ food dollars from foodservice to retail establishments. This meant producing more cuts to retail specifications and fewer for foodservice. This will continue as such spending is unlikely to return to a normal 50:50 split until the pandemic dramatically recedes or until the majority of Americans are vaccinated against the virus.
Companies acted on numerous fronts to protect their workers, at huge expense. Tyson Foods, North America’s largest meat and poultry company, incurred direct incremental expenses associated with the impact of COVID-19 totalling approximately US$200 million and US$540 million for its fourth quarter (ended October 2) and 12 months of fiscal year 2020, respectively, it says. It expects such costs to decline to US$330 million in fiscal 2021.
Meanwhile, Tyson sold far more beef to retail outlets in fiscal 2020 than in 2019, in large part because of the impact of the COVID-19 pandemic on foodservice establishments from March on. Tyson’s retail beef sales totalled US$8.155 billion, up US$735 million on 2019’s US$7.420 billion. Its foodservice sales totaled US$3.669 billion, down US$482 million from 2019’s US$4.151 billion. Beef sales in 2020 were thus 2.2 times larger to retail than to foodservice, versus 1.78 times in 2019.
U.S. processors still face challenges. Most beef companies cite labour shortages and worker protection as the number one issue facing the industry. This was clear from companies’ responses to my annual survey of the Top 30 U.S. beef packers last November. The main issue facing the industry remains labour, says Kazunobu Nomura, president and CEO of Creekstone Farms Premium Beef. The pandemic magnified the labour issue, but it was a major problem long before the virus came to the U.S. Even with a high level of unemployment, packing plants are struggling to run at capacity, he says.
The number one issue is still employee training, engagement and retention, says Trevor Caviness, president of Caviness Beef Packers. The top issue is the challenges created by the COVID-19 pandemic, including labour shortages and varying channels of demand for all products, says Henry Davis, president of Greater Omaha Packing Co. Brian Coelho, president of Central Valley Meat, also cites having to navigate fluctuating demand for products and labour issues related to the COVID-19 pandemic. Higher than normal turnover and absenteeism has made it difficult to operate plants at capacity, he says. Notwithstanding these challenges, processors should be congratulated on how they tackled and overcame COVID-19 in their plants.