Animal handling is a big deal at Kolk Farms. It has to be when you’re looking out for the wellbeing of people and 12,000 head of cattle every day, year in and year out.
Quiet has always been the word as far as animal handling goes, says Leighton Kolk. Cattle, hogs and poultry have all been part of the mix through the years on the family’s farm near Iron Springs, Alta. He carried that animal-handling philosophy forward as he, his wife, Elinor, and family, Jordan, Devan and Megan, took over, phasing out the hogs and poultry to concentrate on the feedlot and cropping. In 1998, the feedlot underwent a major expansion from 6,000 head to its current one-time capacity and finishes out double that in a year.
Read Also
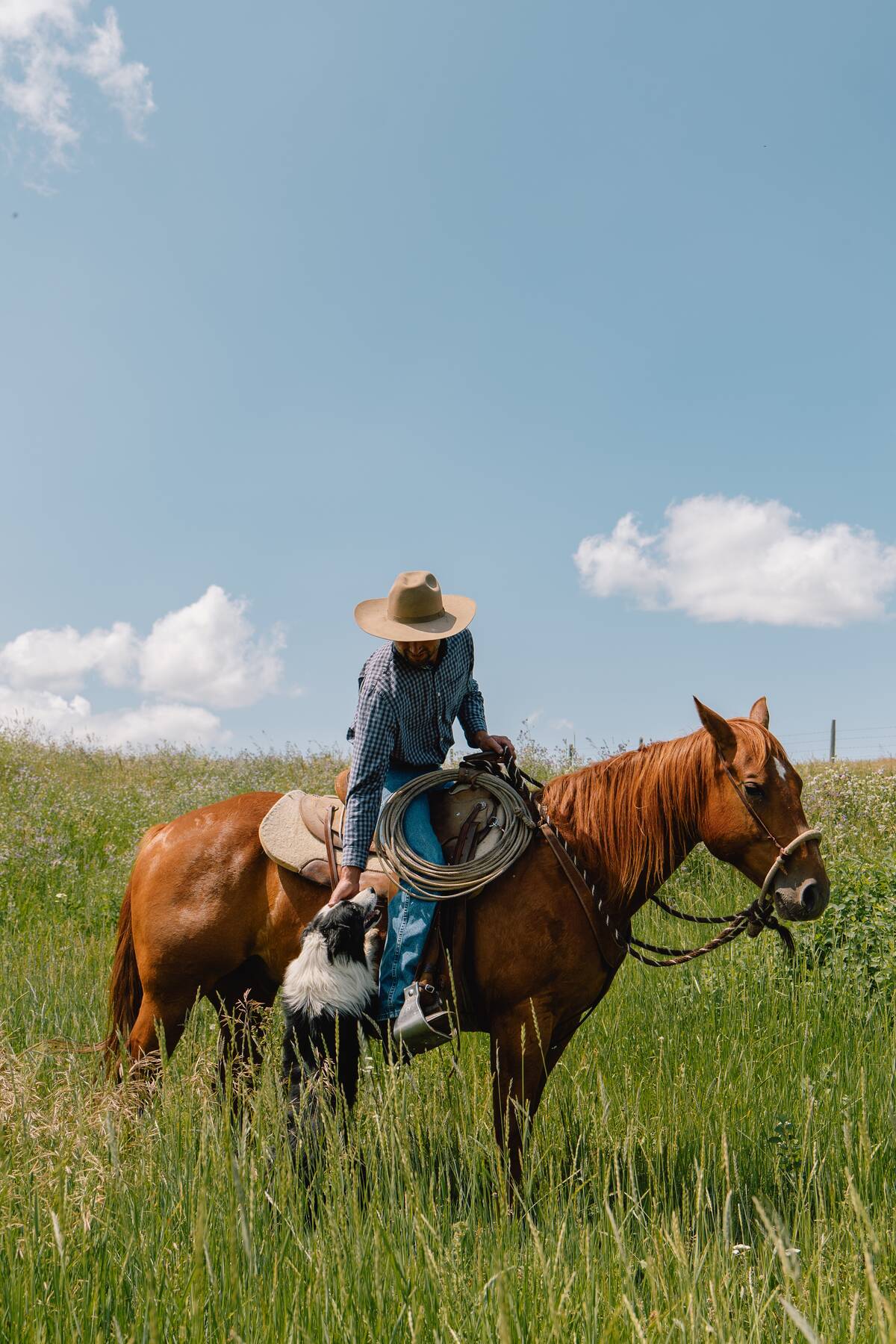
Regenerative ranching sees Alberta family through three decades of ups and downs
Alberta ranchers have found regenerative ranching key to surviving ups and downs of the business
Quiet handling is now part of what’s become known as low-stress handling to encompass new insights into animal behaviour and handling techniques that have been ground proofed in recent years, Kolk explains.
Training on animal handling and safety has always been part of the orientation for new employees. To keep on top of the wave of new science, technology and latest “cow psychology,” Kolk organizes annual staff seminars with renowned experts in the animal-handling field and regular advice from his consulting veterinarian, Phil Klassen of the nearby Coaldale Veterinary Clinic.
“Lowering stress benefits animals and people,” Klassen says. “When cattle are stressed, people are stressed and that takes its toll on both, so the principle of reducing stress should have a positive effect on animal health and productivity. To have a stress-free environment the facilities have to be properly designed and the people trained on how to use them.”
Kolk recently invested in a new processing facility that incorporates the latest in animal-handling strategies which has made it easier for his employees to keep animals flowing through the chute with minimal noise and stress.
Good lighting and radiant heaters hung over the main work areas add to the comfort level because a day rarely goes by when no cattle are moving in, out, or through the chute for routine treatments, says cattle foreman Glen Stronks, who has been with Kolk Farms for 11 years.
The old processing barn with its curved, solid-sided Temple Grandin-style handling equipment is now a dedicated hospital barn.
The new handling system is based on the Bud Williams concept that relies on positioning of the operator to direct the cattle.
The most noticeable difference is at the entry to the processing barn where cattle enter through a wide doorway into a rectangular “Bud box” made from ordinary rail panels instead of a solid-wall tub and crowding gate.
The straight chute to the squeeze and head gate sits at right angles to the box and is again open panels along the sides and on top.
With this see-through design cattle always see the handler who uses eye contact and body position to keep them moving. It also puts the handler on the floor, level with the cattle, eliminating the need for raised catwalks.
Cattle enter on the south side and move freely to the other end of the Bud box. Translucent panels in the north door enhance the open appearance and help disguise the dead end. When they reach the back of the pen their natural instinct turns them back to where they entered.
That’s when they first see the double 16-foot alley leading to the straight chute and the squeeze which is set at right angles to the Bud box. The alley needs to be as close as possible to the gate where they came in, making it the only way out of the box.
Handlers play a large role in this setup. The cattle are processed in small groups. Initially they are given time to move into the box, look around and turn toward the dual exit alley leading to the chute on their own. While this is going on the handler closes the gate to the box, moves to the other side and stands by the entrance to the exit alleys. He never pushes them from behind.
This position takes advantage of the animals’ natural instinct to move around obstacles in front of them that they can see.
Two design elements make it easier for cattle to make the right choice. First is a double alley so animals can travel side by side for about 16 feet or two animal lengths before coming to a gate that swings either way merging them into the single chute leading to the squeeze. Second, any animal looking down the open straight chute can see a clear escape route at the end.
As the first animals enter the alley, others will naturally follow. Stragglers, having nowhere else to go, come along on their own once they think they’re getting left behind.
- More from the Canadian Cattlemen: Diamond 7 Ranch raises cattle with care and compassion
Kolk’s box is sized for 15 nine-weight animals, so the process calls for the next group to be brought in as the last animals enter the double alley.
One-way stops on an overhead rail keep animals moving forward once they are in the chute. The height of the stops and width of the chute are easily adjusted by hydraulic controls to accommodate animals of any size.
Rubber pads anywhere metal meets metal buffer the noise. Even the hydraulic lines are wrapped in rubber and used tire tread is fixed to the floor to improve the footing and dull the noise.
Stronks has noticed that there is very little manure left behind in this new chute, only a couple of shovelfuls at the end of the day before it is hosed down for the night. He can’t say for sure but he suspects this is just another benefit of the secure footing and the general stress-free environment in this new system.
When they first opened this processing barn, sunlight streaming through the south-facing windows created shadows that made some animals balk. They’ve since solved that by covering the windows with plastic and a light spray of paint.
The hydraulic squeeze features a palpation cage with man gates on both sides, swing-away side and bottom panels, and a neck extender equipped with tag readers that end up directly behind the ears of the cattle. A touch of a button is all that’s needed to read an animal’s electronic ID number.
That number is linked to a dangle management tag when the animal is processed into the feedlot and remains the key to reading its performance and health data for the remainder of its stay. Every treatment is entered via a touch-screen panel on the squeeze and can be retrieved just as easily or from an office computer. The program also brings up the feedlot’s protocol for the process underway.
A large screen on the opposite wall lets the person operating the hydraulic controls see the same information as the person giving the treatments.
Cattle can be sorted five ways going out of the squeeze. Air-operated gates to each pen can be programmed to open automatically according to weights from the scale in the squeeze and weight splits associated with each gate entered into the software program. A manual override allows gates to be operated with hydraulic controls on the squeeze.
Stronks says the best way to get cattle to take that last step into the squeeze is to release the first animal into the outside pen down the short alley directly in front of the squeeze. Animals in the chute will want to follow the same escape route.
He keeps an eye on the animals’ body language to gauge how well they’re doing with their handling techniques. Relaxed cattle are alert and inquisitive, not heads up with a one-track mind bent on escape. Playfulness as animals rejoin their pen mates and overall calmness in the outdoor pens tells him that the process wasn’t that stressful. A good experience the first time through sets the stage for future processing days.
Cows continue to be part of the farm operation. The herd winters and pastures on coulee land to the north and is moved to a pasture near the yard for calving in August. This helps a bit to supply calves for the feedlot at an off-peak time, but most of their calves are purchased direct or on contract from ranches and backgrounders. Approximately 40 per cent are sourced from auction markets across Western Canada.
Kolk welcomes questions at 403-738-4500 (office), 403-382-7231 (mobile) or by email.